Porosity in Welding: Identifying Common Issues and Implementing Ideal Practices for Prevention
Porosity in welding is a prevalent concern that usually goes undetected until it causes significant problems with the integrity of welds. In this discussion, we will discover the crucial elements contributing to porosity development, examine its detrimental effects on weld performance, and discuss the best practices that can be taken on to decrease porosity event in welding procedures.
Typical Reasons For Porosity
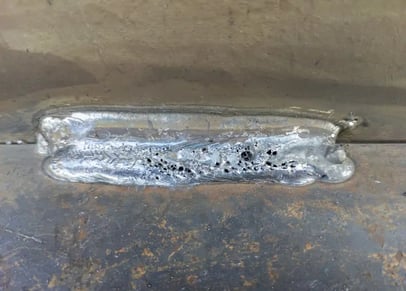
Using dirty or wet filler materials can introduce impurities right into the weld, adding to porosity problems. To reduce these usual causes of porosity, comprehensive cleansing of base metals, proper shielding gas choice, and adherence to optimum welding parameters are necessary practices in accomplishing high-grade, porosity-free welds.
Influence of Porosity on Weld Top Quality

The visibility of porosity in welding can dramatically endanger the architectural stability and mechanical residential properties of bonded joints. Porosity produces voids within the weld metal, weakening its general stamina and load-bearing ability. These gaps act as tension concentration factors, making the weld a lot more at risk to cracking and failure under applied tons. Furthermore, porosity can minimize the weld's resistance to deterioration and various other ecological variables, further diminishing its longevity and performance.
One of the key effects of porosity is a decline in the weld's ductility and sturdiness. Welds with high porosity degrees have a tendency to display lower impact strength and reduced capacity to flaw plastically prior to fracturing. This can be especially concerning in applications where the welded parts undergo vibrant or cyclic loading conditions. Furthermore, porosity can impede the weld's capacity to properly transfer forces, leading to early weld failing and potential safety threats in important structures.
Finest Practices for Porosity Avoidance
To boost the architectural integrity and top quality of welded joints, what details steps can be applied to reduce the event of porosity during the welding procedure? Porosity prevention in welding is vital to make certain the honesty and toughness of the last weld. One reliable technique appertains cleansing of the base steel, getting rid of any kind of impurities such as rust, oil, paint, or wetness that can result in gas entrapment. Making sure that the welding devices remains in good condition, with clean consumables and ideal gas flow rates, can also substantially minimize porosity. In addition, preserving a stable arc and regulating the welding criteria, such as voltage, existing, and travel rate, assists develop a constant weld swimming pool that decreases the risk of gas entrapment. Making use of the proper welding method for the particular material being bonded, such as readjusting the welding angle and weapon setting, can further protect against porosity. Routine examination of welds and prompt removal of any issues identified during the welding process are necessary techniques to protect against porosity and create top quality welds.
Value of Correct Welding Strategies
Carrying out appropriate welding techniques is paramount in making sure the architectural integrity and high quality of bonded official statement joints, building on the structure of reliable porosity prevention actions. Welding methods directly influence the general strength and durability of the bonded structure. One key facet of appropriate welding strategies is keeping the correct warm input. Too much heat can bring about boosted porosity due to the entrapment of gases in the weld swimming pool. On the other hand, not enough warmth may result in incomplete combination, developing potential powerlessness in the joint. Additionally, utilizing the appropriate welding specifications, such as voltage, current, and travel rate, is important for achieving sound welds with very little porosity.
In addition, the choice of welding process, whether it be MIG, TIG, or stick welding, must straighten with the specific click for more info demands of the job to guarantee optimal results. Correct cleansing and preparation of the base steel, along with selecting the best filler material, are likewise crucial components of skilled welding methods. By sticking to these finest practices, welders can lessen the threat of porosity development and create top quality, structurally audio welds.

Testing and Quality Assurance Measures
Quality control steps play an essential function in verifying the stability and reliability of welded joints. Examining procedures are necessary to spot and stop porosity in welding, making certain the like it toughness and resilience of the final product. Non-destructive testing techniques such as ultrasonic testing, radiographic testing, and visual assessment are frequently utilized to determine prospective flaws like porosity. These strategies permit the analysis of weld high quality without endangering the stability of the joint. What is Porosity.
Post-weld examinations, on the various other hand, examine the last weld for any type of problems, including porosity, and verify that it fulfills specified requirements. Applying an extensive high quality control strategy that includes extensive screening treatments and inspections is vital to decreasing porosity issues and making certain the overall quality of bonded joints.
Verdict
In final thought, porosity in welding can be a typical problem that influences the quality of welds. By identifying the common causes of porosity and carrying out ideal techniques for avoidance, such as appropriate welding techniques and screening steps, welders can make certain top quality and dependable welds. It is important to focus on avoidance techniques to decrease the incident of porosity and maintain the stability of welded structures.